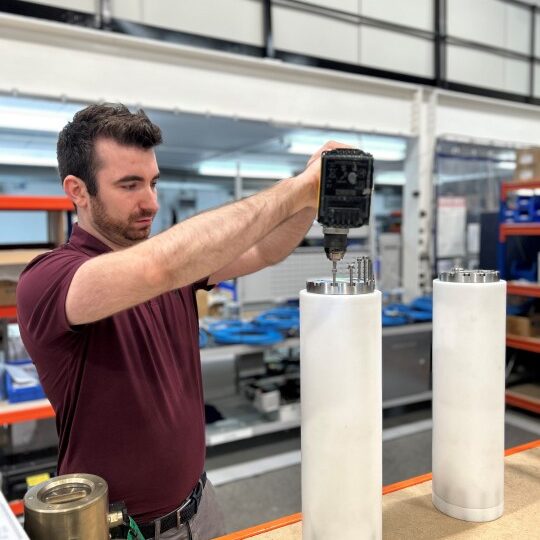
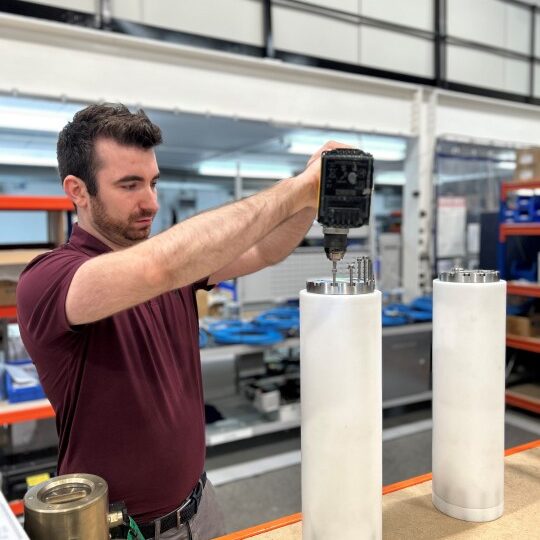
Introduction
The EMTx50 electromagnetic transmitter is a ground-breaking innovation that represents a significant leap forward in pig tracking technology. With unmatched power and a robust design, it is suitable for larger-diameter pipelines where signal strength and reliability are key to precise and quick detection.
This case study will explore the development of the EMTx50, showcasing the collaborative effort of the IK Trax design, production and sales teams and the innovative technology which made this standout product possible.
Background and Objectives
Developing electromagnetic transmitters for larger pipelines is not new to IK Trax – for years, we have led the market with our 3007 EM transmitter. However, digitalisation has led to demands for further flexibility and customisation and an enhanced user experience. To meet these demands, upgrades were required for the transmitter to be compatible with our EMTx Config Android and Windows Apps.
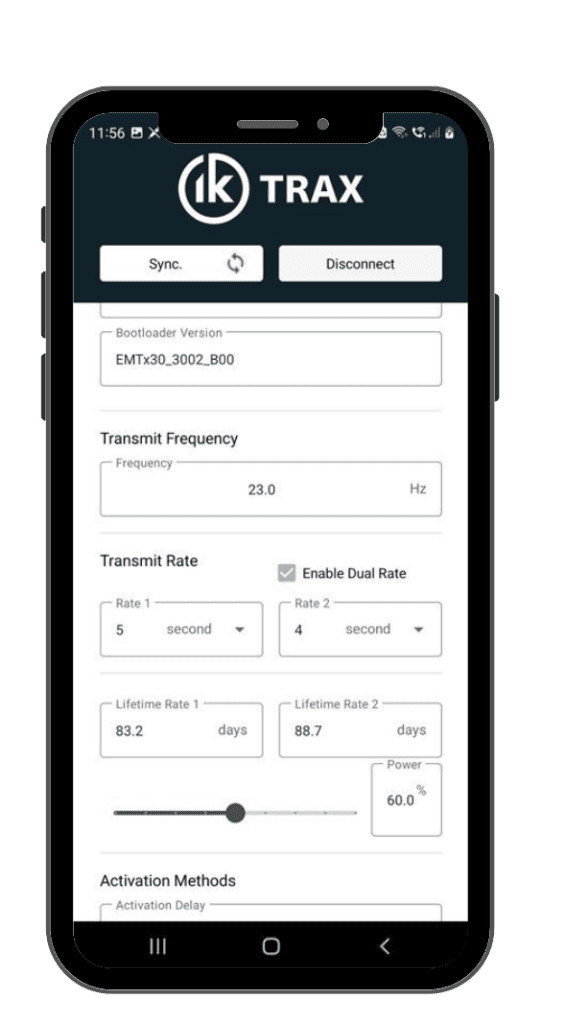
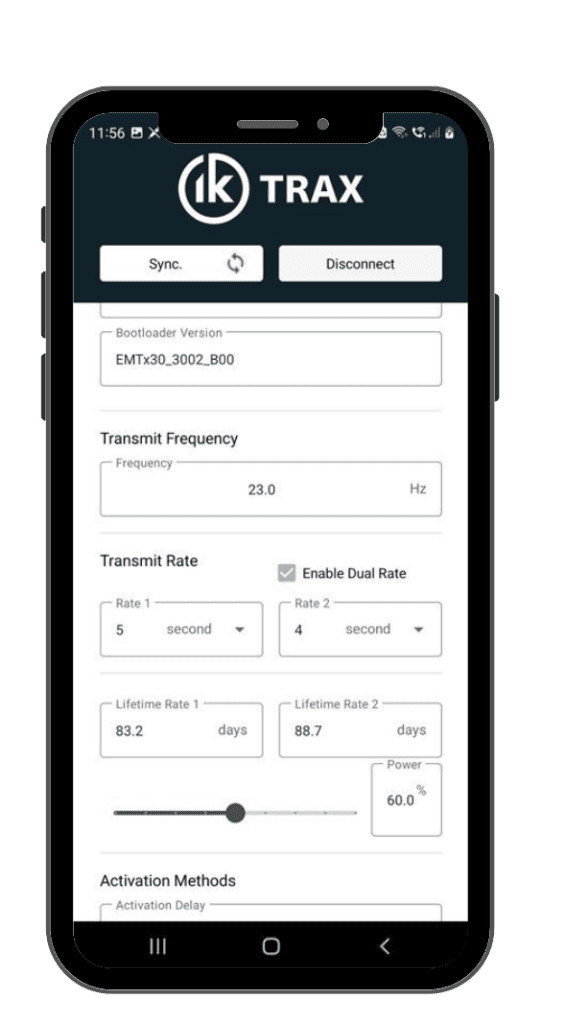
These Apps enable customers to modify transmitter parameters and gain insights into expected battery life, offering them customisation options and an improved user interface that they now expect. Thanks to the composite housing, this can be done in the field without removing the endcaps, removing that extra layer of complexity. Different endcap options are now available to achieve delayed switch-on, allowing the pigs to be loaded before launch without depleting the transmitter battery.
To address the challenges of extra-large diameter transport pipelines spanning long distances across countries and continents, the transmitter performance and power had to be enhanced while ensuring compliance with pressure and temperature requirements and remaining commercially viable.
Design Challenges and Solutions
Designing a housing for such a large EM transmitter presented mechanical challenges. It needed to withstand high operating pressures while adhering to size, cost and manufacturing constraints. Considering that this is the largest EM transmitter we have developed, the unit will experience the highest loads and forces during the operation that we have seen and would have to be designed accordingly. Size restrictions were also a critical consideration; a larger housing would limit the number of pigs that could house the transmitter, reducing its commercial potential. To address this, we conducted an in-depth investigation to determine the optimal size that would maximise marketability without compromising functionality.
To meet the demands of extra-large diameter transport pipelines, we significantly improved the transmitter’s power output, increasing from 1000mV in the 3007 model to 2300mV in the new EMTx50, and, ensuring reliable performance over long distances. Considering the extensive length of these pipelines, battery life was a major focus. The electronics were designed to be low-power, the coil was optimised for efficiency, and the battery pack was maximised for energy capacity. These improvements extended the operational life of the transmitter, reducing the need for frequent maintenance and replacements.
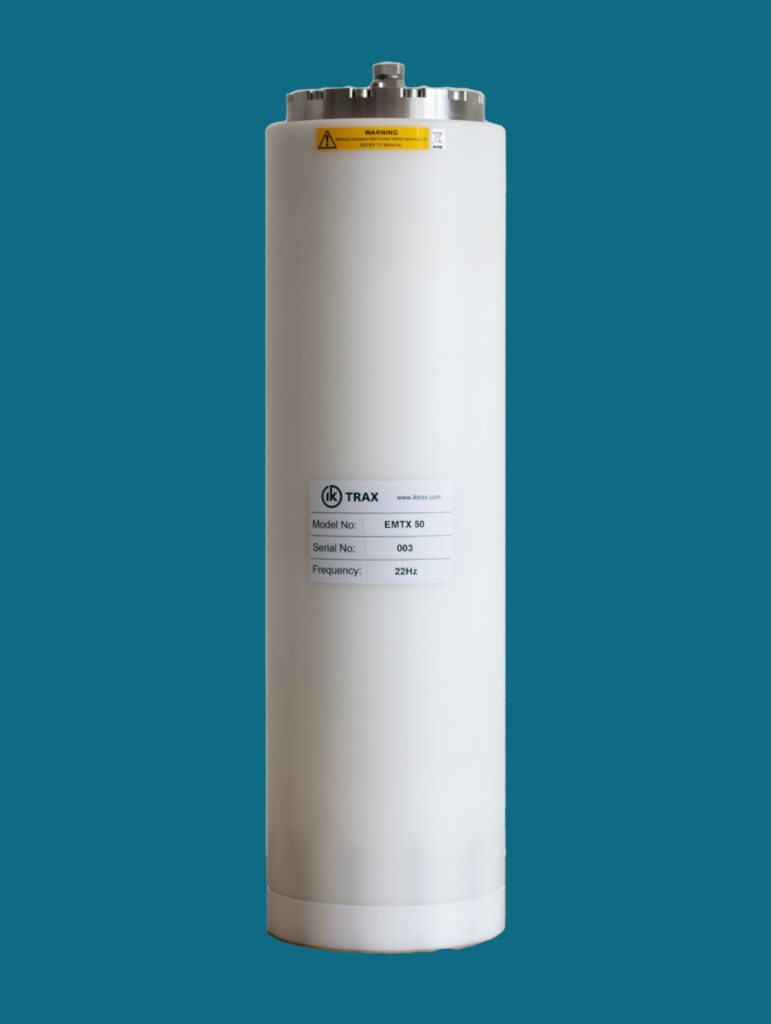
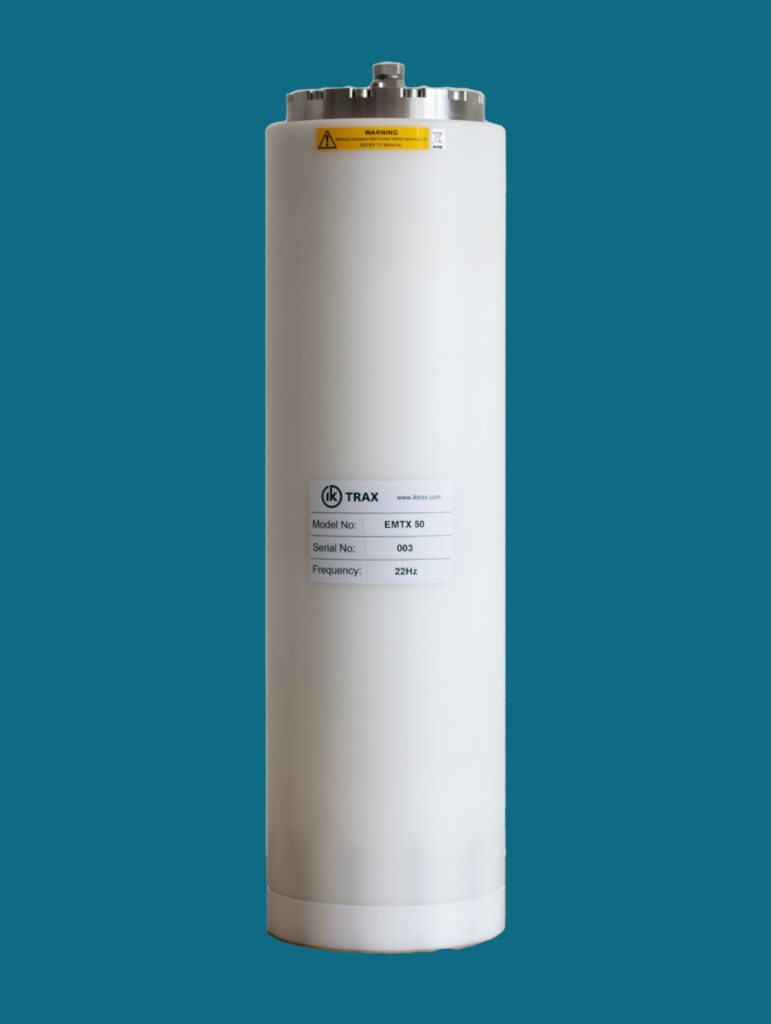
Rigorous Testing and Validation
During the testing phase, we conducted comprehensive assessments to ensure the reliability and durability of the transmitter. We utilised Finite Element Analysis (FEA) and meticulous design calculations to ensure the enclosure could withstand external pressure tests. Once manufactured, the units underwent a successful 24-hour pressure test at 1.25 times the operating pressure. During this test, we closely monitored creep behaviour in the composite enclosure, which proved to be negligible. An internal pressure test also confirmed that the EM Transmitter had a 130 bar internal pressure rating. The EMTx50 was also subjected to comprehensive testing for high and low-temperature extremes, as well as shock and vibration testing. This ensured the transmitter could withstand the harsh conditions it would encounter in the field.
Extensive battery testing was performed at various power levels and pulse rates. This testing provided valuable data on battery performance and longevity, ensuring reliable operation over extended periods. We also conducted thorough yard testing using our test pipes, which have wall thicknesses over 35mm. This allowed us to determine the different detection envelopes achievable with the EMTx50 compared to our existing transmitters, confirming its superior performance.
Ensuring Performance: Collaborative Design and Efficient Manufacturing
We had to employ several strategies to ensure that the EMTx50 not only met but also exceeded the required specifications, and collaboration was key to achieving this.
Our design team worked closely with the IK Trax sales team, which was crucial in determining the optimal size of the EM transmitter. This ensured the transmitter could meet a wide range of job requirements and maximise its commercial potential. Maintaining strong relationships with various suppliers and machine shops allowed the engineers to optimise the design for both cost and manufacturability. These partnerships ensured that the components could be produced efficiently and economically.
For the mechanical build of the EMTx50, the design team collaborated with our technicians, who have years of experience building for the oil and gas industry. Their extensive expertise was invaluable towards developing detailed build instructions and the necessary assembly tooling. This significantly reduced build times, ensuring efficiency and precision in the assembly process.
Conclusion
The EMTx50 demonstrates that with greater size comes increased power. Through collaborative efforts, meticulous design and efficient manufacturing processes, we have achieved a product that meets the demands of modern pipeline tracking and sets new benchmarks for reliability, performance and user experience in the field.